Useful Links
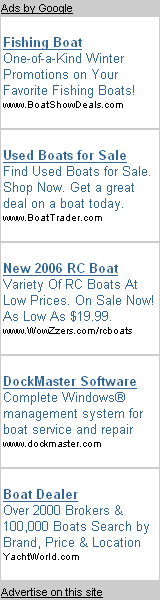
Bayliner Capri 1987 Rebuild
So, here's where we start. 1987 Bayliner Capri. Doesn't look too bad from this angle, huh ?
Shortly after we purchased the boat, we splurged on all new interior upholestry. The local guy we used did a beautiful job, so the thought of trashing all his good work was painful.
Now, the Force outboard, that's another story...
Looking forward. Like the way to 2 consoles sag ? They would flop around when running the boat; all the supporting structure was rotten. I attempted many times to secure things, using bigger and bigger screws, bolts, etc. But, no matter what I did, nothing would hold it together.
Closer view of the port side console. Notice the black areas ? I later found out these were thin, molded plastic covers that would lift off in 1 piece, exposing the gelcoated fiberglass console underneath. On this side, the fiberglass underneath was in the same shape as the black plastic cover. No so on the starboard side..
On the starboard side, the molded black plastic dashboard is very much different in geometry from the fiberglass console underneath. My best guess is that they pre-assembled the wiring and instruments into the black plastic overlay, and then could just drop it in place, once the assembly process was ready for it.
There was no way for any collected water to drain away from this area. So, this was all rotted.
So, get out the sawzall and get to work. In this view, the rotted decking is coming out. I stopped to pump the remaining few gallons of gas out of the tank. Wow, what a crummy design. Aluminum tank sitting right on the bottom of the hull, surrounded by bilge water. No wonder it started leaking.
Rear deck is out. As I suspected, the stringers are shot too. I found out later that the wooden stringers were not even bonded to the hull !! To remove them, I cut the top of the 'glass off of them AND WAS ABLE TO LIFT OUT THE SOMEWHAT INTACT WOOD. Nothing was bonded together.
Yeah, they were rotted too. And the foam.... Completely waterlogged everywhere I found it. Literally, hundreds of pounds of saturated foam came out of this boat.
For some reason, they chose to build the seat bases much stronger than anything around them or supporting them. Yeah, soaked foam under there too.
After grinding it all down, here's whats left. Gotta wear a good mask when doing this stuff. Tremendous amount of dust gets generated.
Here, they're bonded in place. I found good solid Ipe mahogany 1x6 stock for the new stringers and braces.
The stringers, cross braces, and transom knees are in; 3 layers of epoxy and 9oz. fabric holding it together.
I decided to work from front to back in the rebuild. There's lots of tricky woodworking to do so that it all fits and STAYS together.
Looking forward between the consoles, the structure is coming together. All the big parts are tabbed in and ready for epoxy and cloth. Take a look at the patch I needed to make for the dashboard. It was originally sawed right thru from the factory to make room for the wiring. No wonder it sagged...
The hull was joined to the deck with only pop rivets and caulking. There were a few places where leaks developed. This seemed like a good time to do this in a better way too. Here, a strip of plywood is first bonded accross the joint with 3M 5200, left to cure for week, then fully filleted and 'glassed in.
Yeah, that was all rotted too. I laminated a bunch of scraps of the Ipe into a block and glassed it in.
It took quite a bit of temp bracing to pull all this back into shape. But, using the walk-thru windshield as a gauge was helpful. All plumb and square now.
Epoxy had formed a bit of "blush" when it cured. This was easily cleaned up with hot water and a kithen sponge. I put a coat of white paint on the upper area of the console. It'll need more but looks good so far.
Ready for a coat of paint. I'll match up a blue, close to the color of the interior upholstery.
Not bad. It came out as good as I could have hoped. Its getting dusty already, but it still makes it seem like I'm getting somewhere.
The old black plastic dash board overlays were in bad shape, but I decided to use them as a mold to make new fibreglass ones. Here, the first one is molded.
Here's the finished part. It took some fighting to get it out of the plastic mold, mainly because of all the complex angles and shapes.
Finally they're done. The 2 parts I molded are now bonded into place and faired into the surrounding structure. The painting was tedious; 5 coats of black, lots of wet sanding and polishing. I got a little crazy and added the mahogany inlays (with 7 coats of varnish, more polishing....) but the end product is worth it. It will kill me to cut holes for gauges, switches, steering,etc.
Continuing the reinforcement of the deck/hull joint. Here's a question... why would they cut away so much of the side panel ? Yeah, its covered with an upholstered board, but cutting away so much of it really weakened it. Why....
Badly bonded plywood strips that were intended to provide backup for the upholstered panels. This also had to support the weight of the side windshields. The whole thing used to flop around when on the water. It all needs to come out, and be replaced with something stronger
Here I have dry fitted a plywood section to give some stiffness to the sides. Once its all glassed in,it should stop the side windshield glass from flopping around.
Here the plywood panel on the drivers side is completed; Fully glassed in. There is an upholstered panel that attaches to this. This adds a lot more strength.
Before glassing in the next section of plywood decking, I glassed in a section of 3" PVC pipe cut in half to allow the flow of any bilge water from the bow area directly back. The original design had a removable deck panel presumably for under-floor storage. It was always the collection point for any rain or splash water that made its way into the bilge; useless for storage. I intend to fill the section with flotation foam so the glassed in pipe will allow drainage and protect the foam.
For now I'm leaving the center section open; where the gas tank goes. It will give me better access to the transom.
Also had a chance to try installing some of the pour-in foam. This is good stuff. It expands and fills the cavity under the deck real good.
I cut away a section of the splash well to get access to the transom. I was undecided at first about what to do with this. But since every piece of wood in this boat was rotten, why would the transom be any better ? It has to come out.
These boats used a stepped transom, meaning that it doesn't extend all the way accross the stern. While glassing in the stringers I also glassed in these knee braces. I was not certain back then what else to do, but at this point I'll cut it all away and build something better.
Look closely... The transom is made from 1 piece of 3/4 plywood... Only 1 thickness... oh boy... I hope to put a new or late model outboard on the boat when I'm all done. The new 4 strokes weigh a good 100lbs more that the old Force clunker. Yeah, gonna need to beef this up... substantially.
View looking aft; the inner skin and the plywood has all been removed. Yeah, it was only 1 thickness of 3/4" plywood clearly not marine ply; there were a number of voids. That's all that supported the outboard....
Double thickness of 3/4" plywood. The reinforcing knees are a total of 3 thicknesses of 3/4" material; 2 of ply, 1 of the Ipe material used on the stringers