Useful Links
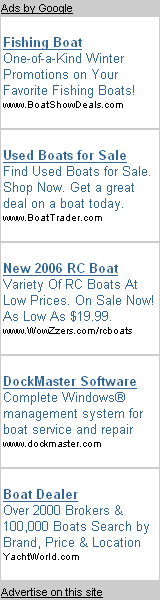
76 Grady White I/O conversion
As a school teacher, a great summer project; or 3. After 3 years of accumulating the parts and finishing the fiberglass work, it's finally ready for sea trials.
Here is the original 4 cylinder. She ran fine, but could only push this old Grady to about 28 mph; a heavy boat for a little 140hp 4 cylinder.
I removed the old 4 cylinder I/O. Used 3/4" ply to reinforce the stern and give the the 3 pieces of 3/4" ply that was used to fill in the old hole something to grab to. I used West epoxy and SS screws to attach the filler plates to the large backing plate, then used polyester resin and glass to coat over the entire backing plate, then 3 coats of gelcoat to seal.
Lots of room now for the the required lines for the outboard. I fabricated a plywood base for the oil tank, then used epoxy resin to seal all sides. This was then bolted to the stringers in case I should need to remove it. All holes penetrating the transom where over-drilled, then sealed with epoxy. No wood is exposed to the potential of water penetration. All the ss bolts securing the motor bracket were drilled out, then filled with epoxy; then redrilled to fit the bolts. The hardest part of the retrofit, was the sanding smooth of the old transom, and then the 3 coats of gelcoat to seal the new fiberglass covering the backing plate. Spraying on the inhibitor, allowing time to cure, then washing off all the sealant to prep for another coat of gel was a long process, but well worth it in the long run. I can now spray down the entire inside of the old motor well for rinse-down with no "unsealed" wood being exposed.
One thing I had not thought about with the engine conversion, was the steering, guages, shifter, and electrical. This slowed me down while I did research on the electrical for the Yamaha system. Also, the original dash board had so many holes that I had to figure on some way of mounting all my guages that I wanted, and still make it look decent. White plexiglass answered the call. I cut out all the offending fiberglass from the dash board and fitted white plexiglass to the top half. I arranged the guages and water-tight switches, then had to figure out how to make it water-tight. I used 3M 4200 sealant. I placed a bead all around on the original fiberglass; placed a piece of waxed paper over the entire dash area, then placed the plexiglass on top, and gently screwed it down, squeezing out the excess 4200. I allowed this to cure for 3 days, then removed the plexiglass, trimmed the edges, and low and behold, a custom fit, water tight gasket for the dashboard.
The hydraulic steering was another problem. The helm pump sticks out about 6 inches, which now placed the steering wheel in interference with my new Yamaha throttle and shift lever. I wanted to recess the helm pump into the dashboard. I built a woooden brace to mount the pump to about 4 inches into the dash board. This wood was sealed with West epoxy, then screwed into place. The helm pump now only sticks out about 2 inches, thus giving me the shifter clearance needed. Once the pump was installed, I cut another piece of plexiglass to fit over the helm pump and cover all the offending holes. I could now locate the ignition switch and begin all wire runs.
Name plates will be added to each switch. Room was left on the dash board for an hour meter and temp guage (to be added later). Current guages include tach, fuel, volts.
Well, its been over a year and the only problem is really the outboard. Seems I bought a piece of junk. The boat retrofit has been great, but getting the motor to run is another problem. its's now Oct '08 and have spent the last few weekends working on the cooling, fuel, filter, etc. Gotta love this new ethanol!!!