Useful Links
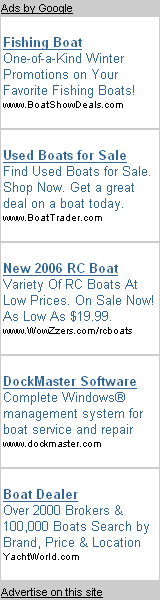
Project 1600 Capri Hard Top
This is the boat as originally outfited by Bayliner. I really like it and we used it this summer to get a feel for if I should make a hard top or not. I realized a hard top with steeper incline windshield and higher top will give more usable space inside and more protection from the elements than the factory Navy Top.
First step was to do a photo mock up of my idea to see what it would look like on paper. This photo was done with MS Paint.
Took about 4 hours on a Saturday afternoon to measure, cut and assemble this simple cardboard mock up. But it does give a much better impression of what the finished product will look like.
One of the advantages of a cardboard mock up is getting to sit inside and see and feel the actual dimensions. I made the top 3" higher than the photo mock ups, and my head still just rubs the top. By lowering the floor between the stringers 3 inches, there will be full headroom for my 5'8" height.
I didn't do the windshield frame, but I did make the V shape on the top to mach the windshield angle. At this point I am happy with the look and feel.
Another view. When compared to the photo mock up, the card board version is taller. It also does not have the V shaped windshield on it, and that will give it a longer appearance.
Front view. The sides are slopped in a little bit to match the curve of the boat.
Next step is to go buy the foam panels and start fabrication!
Tested polyester resin on the common pink rigid styrene foam and also polyisocyanurate foam. Both available at the home centers. Polyester resin melts styrene foam, but not polyisocyanurate foam. Polyisocyanurate foam is what surf boards and boats are made from. The difference between what I tested from the home center and what you buy for surf boards is the density. Surfboards are typically about 5lbs density foam, the stuff from the home center is 1 or 2 lbs. A huge difference in price too. Using the 1" thick home center version will cost about $60, the 5lbs stuff about $400 plus. We'll see how well it works.
I tried pealing off the cured resin from the foam, and it pulled the foam apart, so the resin does adhear, the foam is just not very strong.
Removed the windshield and side glass. It came off easy with about a dozen or so screws. I put two layers of cardboard in the cuddy and stored the windshield there for safe keeping. Then took more measurements, this time more exact and updated my sketches.
With the windshield off, I was able to lay out how the two windshield panels will sit on the dash. Hard to see in the photo, but there are pencil lines that intersect in the middle of the boat at a 34* angle. This is the center line of the boat, but the boat is not entirely symmetrical. The port side is 1/2 wider than starboard measuring from the center line. The hard top will have two windows in the windshield where the original windshield had three.
After cutting up some 1/4" plywood and having problems, I decided to use styrofoam and epoxy. Had to glue up two pieces to get the size needed to cut the side walls out of. Using special styrofoam construction adhesive available at the home centers. Stuff takes forever to dry. Put some weight on the seam while it cures, and to keep it from blowing away.
Cut both side panels and threw on the cardboard top for a trial fit. Glad I did because I had the sides tilted in too much. Going with less of an angle.
This is about as much as I got done before putting the boat away for the winter.
Sprint has come and work is continuing on the project. The top will be removable. To do that and be able to attach it well, the bottom perimeter of the top will be 3/4" fir. Bolts will come up from under the gunnels and into the wood where T-nuts are epoxied in place.
The port and starboard boards have the T-nuts epoxied in so that they can't come loose later on. The same treatment is given to the wood supports under the windshield. A total of 10 bolts will hold the top on the boat.
I was having trouble finding a good glue to attach the foam panels together, or attach anything to the foam panels. Then I gave Gorill Glue a try. Gorilla glue works very well. Here the wood base supports are glued to the foam side panels with gorilla glue. The glue expands when activated with water and squeezes out the sides. But it holds really well.
The roof panel required gluing up three foam panels to get a piece large enough to cut the roof out of.
It was a hot day, so I brought the glued up panel into the house to measure, mark and cut it.
One good thing about trial fittings; you learn if it works for you or not. In this case I learned that the roof panel needs more reinforcement than I anticipated. So to give it more strength and to not rob head room, I decided to bow the roof.
Using a 4 ft level, I drew lines spaced the width of the level (about 3 inches). Then using the razor knife, jut 1/2" deep scores down the lines. This made the roof panel more flexable and easy to bow without having to fight it.
Cut these roof supports out of 1x4" and ran a 3/8 radious bit in a router over them to remove the sharp corner. This will make it easier for the fiber glass to lay over the supports. 'Glass does not like to make sharp bends.
My Daughter Amber is a often my helper on projects. Here you can see the duct tape used to attach the roof supports while fitting the top to determine the best location for the supports.
The roof is resting in place. I realized that the bow in the roof gave 3" extra headroom. The whole top was getting rather tall, so I cut 3" off the side panels. That returned the headroom back to what it was, and makes the top look lower and sleeker.
The roof supports can be seen here. The space between them is where clear headroom is needed for standing. There is about 5'9" of headroom. 6'3 if you include the possability of lowering the floor to bilge level.
Two tension lines keep the top square while the front windshield panels are cut and fit. Making them run from the roof support to the sides rather than diagonal across the boat leaves the cabin open for me to walk in and out.
The base of the windshield is made the same as the side panels. Wood base with T-nuts epoxied in place, then 1 1/2" vertical foam section.
A good view of the leading edge of the windshield. One more windshield panel to make, then the whole top can be glued together and removed as one piece to cut windows and start sanding and shaping.
Opened a can of Great Stuff home expanding foam sealer. It did glue the styrofoam together, but stayed soft and not as strong as the Gorilla glue. So I won't be using this to fill gaps on the top.
I knew from gluing panels together with Gorilla Glue that it foams up and cures very hard. So I wanted to see just how much I could get it to foam up so it would fill gaps where the panels meet. I mixed about a teaspoon full with 3 drops water in the plastic jello cup. After 15 minutes, it had expanded to what you see in the picture. It still cured very firm, much harder than Great Stuff. So when I glue up all the top panels, I'll mix some water in with the glue so it will fully expand and fill any gaps. It pays to test!
Trimmed the roof to the right width and glued on the roof supports, then glued the roof panel to the side panels. Angle braces were added to the rear in line with the roof brace for lateral support. These angle brackets are about 8" wide and 16" tall.
Been about two weeks since I was able to work on the top. Finally had some time to work on the boat today. Got the windshield panels glued in.
Used a lot of glue on the windshield panels. So some rubber bands stretched around tooth picks were needed to hold things in place. Otherwise the expanding glue could push panels apart.
There was a small gap in the front of the top. Cut a piece of foam and glued it in.
Next, the top comes off the boat for sanding and shaping.
Top is off the boat, the boat is outside. Now its time to start sanding and cutting.
Spent some time cutting the windshield openings. Started a bit smaller, then got inside and checked out the view. It was too small, so I cut another 2" off the center side of the windows, then two inches off the top, and one inch off the outside sides. Now they are big and the view is much better.
The side windows I made a little shorter in length than originally planned. I also cut off the sharp leading edge, because it wasn't really of any practical use, although it looked nice. Cutting it short makes the opening larger quicker when sliding the window to the rear. Plus there is more support under the windshield outer edge.
All windows cut. Both the front two and side two windows are exactly the same size, even though the top is not 100% symetrical. That way when I have the glass cut, the shop will only have to cut two size windows, not four.
The top is looking and feeling light and airy. Not at all closed in. I like the fact that I have a good field of vision from inside.
The windshield windows need to be in frames. Started with 1x4 pressure treated pine. Ripped down to 1x3, then cut to frame the window opening.
Here are the finished frames. Ran in to so many problems. First, could not get the latches I needed to seal them closed. Second, they are way heavier than expected, and third, I don't like the looks of them. So they are now in the recycle bin. Decided to go with windsheild that will not open for simplicity.
Before applying the fiberglass, holes were punched into the foam about every 1-2 inches. Hopefully this will allow the epoxy to get a better grip and delaminate. When the first coat of epoxy was squeegeed on, I forced it into the holes.
This is a test of the fiberglass and epoxy I ordered. Its a piece of 1708 biaxial. That means a 17oz weave at 45* with an 8 oz mat behind it. Rather heavy stuff, about 1.5 lbs per square yard. But this test showed it is very tough stuff, I hammered it , poked it, and eventually stuck a 1/4 screwdriver through it, but that was hard. When I started tearing it apart, I found the puncture holes had epoxy in them from 1/4 to 3/8 in deep.
Wow. Resin gets hot as it hardens, so hot it melted the plastic cup the unused portion was in.
Worked the roof a bit to get the dip out. This is as good as I'm willing to work it. Anything more will be fairing compound after glassing.
This is one piece of 1708 biax, 10ft x 50 wide. Does most of the roof and sides. Wrapped some around all openings and rear side panels for extra strength. This one layer has made the top incredibly strong.
This section of 1708 glass wrappes around the starboard side of the top. It looks cloudy because I waited too long and the resin started to thicken and harden. Thick resin will not saturate the glass, and the result is only a partial connection to the foam. Not a big problem here, but something to be aware of going forward.
The corner where the roof meets the side came out fairly good. Had some trouble with saturating the glass on verticle surfaces, but it came out good.
Finished covering the entire roof area, and also the lower windshield area. Just have to fill in the gap between top and bottom.
Used Cabosil (micro glass hollow balls) to thicken the resin to putty consistency. Made fillits along the windshield support. Planned to do this everywhere on the inside, but after doing this, I realized it is just too much work. Will save the Cabosil to make fairing compound.
My Daughter and Daisy the dog are helping wash the blush off the top before starting todays work. The anime blush comes off very easy, just a little dish detergent and a soft scrub brush is used to rub the top, then a blast from the garden hose and it dries clean and wax free.
Here the top is standing on end. You can see the overlap of the glass. It will take a bit of fairing compound to eliminate the seams where there are overlaps.
Was cutting out the excess foam that squeezed out from the joints where boards meet foam, or foam meets foam. Just wanted to get a nice clean corner for the 6 oz glass to fit into.
The rib added to the center section of the windshield is covered with a wide piece of 1708 glass. The result is the front of the top is incredibly tough.
I found that by just soaking a disposable brush in a cup with 2" denatured alcohol, it will keep working for a long time.
I'm using the 1708 biax top and bottom on the rearward most part of the top. It's so much easier to fit the cloth in, mark with a Sharpie marker, cut and trim and make the corner cuts for overlap. That way, after soaking the cloth with resin, its easy to put back in exact location.
the interior is much harder to glass than the exterior due to the more complex shapes and supports inside.
This area on both sides were made from a few pieces that overlap. Used a 40 grit disk to remove some of the high areas where they overlap prior to applying fairing. Needs more grinding...
The ceiling between the front and rear cross supports is glass in using 6oz cloth. It looks clear for the most part. Some blochy areas are because there is not enough resin on top, not from air underneath.
Some areas have two and three layers of the 1708 overlapping. The high spots were sanded smooth in prep for fairing compound.
It is hard to sand in the corners with the little 5" disk, like this window corner. Will have to finish with the 7" and add a little mat and sand again before fairing.
The wood strip at the base is wrapped in a 6" wide piece of 6oz glass. After the anime blush was washed off, it looks like there is not enough resin on the top of the cloth. The cloth has resin under and inside, but the top side is looking a little dry. Will have to brush on a coat of epoxy to seal it well.
This is a closeup of the 1708 biax on the side. The weave in the glass has come to the surface. I think rolling on a layer of epoxy will smooth it over so sanding will not expose the glass.