Useful Links
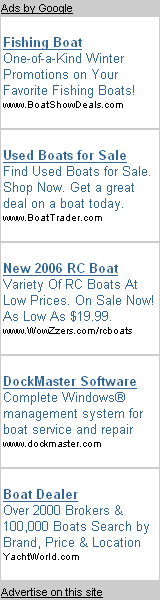
Raising the Barn Roof
We haven't located any information that can help determine when this barn was 1st built. And there are several things about its construction that we are really puzzled about. Like:
The framing is pegged post and beam, but the siding is 'modern' tongue and groove 'car siding' not the wood board and batten siding commonly seen on these old buildings.
There are numerous mortises in the posts that are not used? Has framing been removed? Has the barn been remodeled? Was it built from left over parts?
Of course I didn't take any before pictures. But the center point of the barn roof has sagged 3 1/2 inches. At the same time the west wall at the plate has bowed out about 5 inches.
This is multi part operation. The first two parts of the project are to raise the center ridge board back up, WHILE at the SAME TIME pulling the side walls together to correct the bow out in the West wall. (Thats what the yellow tow straps running across the middle of the picture are doing)
The east wall is straight, plumb and seems to be well braced to the floor. The west wall brace either failed or whoever put up the basketball net tried to remove it. The lack of a brace on the west wall has helped lead to the problems. We need to replace that bracing with new braces that will prevent this in the future.
Here are the 3 'posts' we built to jack up the center of the roof. More details later..
Also a nice view of our Ventilated roof...
At the same time we raised the center of the roof, we were pulling the side walls together. We used 2 -20 foot tow straps to reach across the barn from wall to wall - almost.. Here you can see the 2 ton rated come-along coupled between the cables from one post to the 20 foot tow straps that run to the other side of the barn.
During the process of jacking up the roof, we were raising each jack 1/4 inch, then tightening the come-along then raising the jacks again, tightening the come along.
Eventually we raised the ridge 4 inches and pulled the side in 5 inches.
One of the challenges was how do we get a good hold of these 6 x 6 posts at the center of the walls so we can pull them together? Nailed on metal straps or wood blocks won't withstand the forces involved.
Also, we are not dealing with minor loads and forces here. The come-along we are using is a 2 ton capable puller and the two yellow tow straps are rated for over a ton of force each. So we are able to put almost 4000 pounds of pressure on these posts. The way in which we connect to them needs to be able to handle that load with a safety margin.
We ran 5 loops of 3/8 steel cable behind the posts at each side of the barn. I bought a 50 foot package of cable, cut it in half and wrapped one 25 foot piece around each post and double clamped the ends together. 3/8 cable is good for 1000 pounds per stand so these 5 strands are enough to hold our load.
As you are setting this up for yourself, keep safety in mind, We purposely used these yellow tow straps instead of chains or cables not because they're cheaper. But, because we wanted something with some give or elasticity to it so it would keep tension on the building all of the time. But that elasticity comes at a price, if these straps come loose, because the cables or puller, etc failed, the straps are going to recoil so hard they will take out the side wall.. and ANYTHING in their path.
Our barn roof has a center ridge board that gives us a great place to push on to raise the roof, but that ridge board is 16 1/2 feet above the haymow floor. After talking with a local carpenter we decided to go ahead and place the jacks on the haymow floor after using bridge planks to spread the load. Additionally we identified where each jack is and cut and jammed a post under the floor to transfer the load to the concrete ground floor. We now have a direct load path from the jack to the ground.
Once the bridge planks were laid up and we had the jacks in place we measured 14 foot 3 inches from the jack to the ridge.
We purchased 4 - 14 foot 2 x 4's for each post and screwed them together with 3 1/2 inch screws to form a 3 1/2 x 6 1/2 box. We did this so the grain of the wood was alternated and we had less concern about the posts bending under load. We also were able to align and adjust the 2x's as we screwed them together to get a very straight post. Try finding a 14 foot 4 x4 or 4 x6 at the lumber yard that is straight.. (Small Photo inserted lower right)
Each post then had a 2x4 installed on the bottom along with a steel plate that rests on the jack. These help distribute the load and also prevent the jack from crushing into the wood. (Small Photo inserted lower Left)
Each post was lifted up on top of the jack and raised up against the ridge until snub with the jack. We plumbed each post in both directions. One thing we could have done to make this safer was to attach the top of the post to the ridge. We had a couple of situations where when we raised one jack the others became loose and the posts moved.
Out of our available stash of bottle jacks we used 1 - 20 ton and 2 - 12 ton jacks. These were by far larger than they needed to be. We could have gotten by with 2 or 4 ton jacks. The 20 ton was under the center post and perceived to have the largest load, but we could pump it without using the handle, just our fingers could operate it.
At the ridge we situated the posts such that 3 of the 4 2x's are in contact with ridge board. We had previously tied the trolley and track off to one side so we could get the posts in place.
(We later figured out that we needed to remove the track because with it pulled off to one side it would interfere with the installation of the additional bracing and we couldn't let it drop back to center because the posts are in the way.)
Well, I forget the during pictures, but this photo is a good one to explain what we did.
The original roof framing is 2 x 6's on 24 inch centers and the span is over 17 feet. Needless to say the barn roof was also a little sway back. We decided to add 2 x 8's originally to every other rafter, or 4 feet on center for the 2 x 10's (when we went shopping for 18 foot long 2 x 8's we realized that the 18 foot long 2 x 10's were only $1.50 more each, so why not install the extra lumber.)
So, we cut and added a 2 x 10 to every other rafter. Getting these in place was a 2 man job with three ladders. We actually had to cut them short and then once we had the new rafter in position we jacked the end at the plate up and added a 2 x 4 under the new rafter to hold it up. We also extended the 2 x 4 out to the edge of the 2 x 10, hoping to prevent splitting in the future and also to transfer the load back to the 6 x 6 plate.
This may not look like much, but its a life saver when it came to figuring out how long to cut each of the new rafters.
This is some scrap MDF that we cut the same width of the 2 x 10's (9.5 inches) and we cut the left hand piece to fit at the plate and the right hand piece is cut to match the ridge beam.
We attached one end of a 50 ft steel tape to the one block. We would clamp it in place next to the existing rafter. Take the tape and the other block up the ladder to the peak, measure the distance to the edge of the block. Transfer these measurements and lines a 2 x 10 and presto, you have an exact fit.
This was especially helpful because we did not have to figure out to I measure that from a point to a point and then transfer that to the 2x10. It basically eliminated measurement errors.
OK, so someone will probably say we went over board on the braces, but, its not going to go anywhere..
Once we had all 14 of the new rafters in, we used construction glue and 16D nails to attach the new rafters to the old ones. Many of the old rafters were bowed and we had to use some long reach bar clamps to pull the two rafters together before we nailed them together.
Because we have a basketball goal at one end of the barn we needed to leave enough head room for them to play ball and, we didn't think we needed to brace every rafter 1/2 way down with a 16 foot 2 x 6. So, what we finally settled on was to cross brace four of the new rafters that were in the center of the building with 16 foot 2 x 6's that are 5 feet down from the peek. Then all of the remaining rafters got braced with an 8 foot 2 x 6 that is about 2 1/2 feet down from the peak.
When we attached the new braces to the existing rafters, we used 1/2 plywood gussets, like you would when building a trussed rafter, to attach them. We used construction glue and sheeting staples (7/16 crown by 1 1/2 long) to attach the plywood.
Because the 2 x 10's are 4 inches wider than the existing 2 x 6's we attached the braces to the new rafters by lapping them on the edge of the 2 x 10 and gluing and screwing them in place.
For each of the rafters with the 16 foot cross ties we also ran a 2 x 6 vertically in the center that comes up under the ridge board. These we joined it with 1/2 inch plywood gussets, glue and staples.