Useful Links
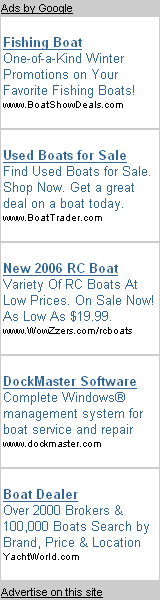
New Steel Roof
We have not been able to determine the age of the barn, the neighbor thinks its related to their house that is 100 years old.
Well this is not the original roof, but it has been on here for a LONG time. Lots of broken and missing shingles, etc.
The original plan was to just install 2 x 4 purlins over top of the existing shingles and then screw the new steel roof to that. WELL..
Once I took the ridge cap off and cut back the shingles and sheathing for the ridge vent, the plans changed.
Actually the fire happened in 1999 or 2000, but the damage is still on the barn. As we pulled the ridge back we were greeted by this. The main ridge board is charred for a good 10 feet and you will notice in this picture and also in some of the 'Jacking up the roof' pictures that there is OSB on one side of the roof.
The story is that a previous owner was burning brush or trash near the barn and caught the wooden shingled roof on fire. It required the fire department to stop it. One section of the roof about 10 feet by 20 feet has been totally replaced. And there are damaged spots all over the roof
Once we got the roof stripped down we found that there was fire damage ALL OVER the roof. even on the other side away from where the fire started.
This is a composite picture, not all of that damage is in one part of the roof.
What changed our mind about stripping the roof was two things:
1. When we cut back the ridge the mess from that coupled with the fact that walking on the roof loosen untold 'trash' we figured we couldn't get the purlins installed without there being mounds of loose shingles laying against them before we were done. Also we would have had to trim off any overhang of shingles on the eaves and gables.
2. Our carpenter friend, each time we talked to him, asked if we were going to strip the roof. There has to be some wisdom there that we are missing, and he never has given us an exact reason, but now with the roof stripped we can work easier and know what 'lays beneath' the roof.
Here I am with a rock climbing harness on roped to the peak of the roof with a shingle stripping shovel removing the previous patch work. Because we are installing the purlins we don't need to remove all the nails, if we were going with asphalt we would need a smooth clean deck. But, the purlins hold the steel up off of the deck and away from the nails.
It took about 6 hours per side, 18 feet by 34 feet, to strip the shingles. Then it took my wife about the same amount of time to move the rubble to the burn pile, thats as far from the barn as you can get.
So about 24 person hours to strip and clean up.
Now we get to install the 2 x 4 purlins. To make the 32 foot width we decided to go with an 8 foot 2x4 in the center and 14 foot 2x4's on each side, overhanging the gable end. We will snap a chalkline once all of this is installed and trim the purlins to length.
Somewhere in the installation manuals for the steel roofing I read that you need to attach the 2x4 purlins to the framing with 60 D - 6 inch long, ring shanked nails. Well this desk jockeys arm is not up to hammering hundreds of these nails in Soooo.
We picked up a used hand or palm nailer on eBay. Its kind of like a mini pile driver, you put the nail in the nose and when you push down on the body of the tool it starts to pound the nail in. It worked REALLY slick and we got all of the purlins installed
And somebody is asking, why do you need 6 inches nails for?? Well the 2x4 purlings are actually 1 1/2 inches thick, the existing roof boards are 3/4 inch, so you have 2 1/4 inches of lumber even before you get to a rafter. A standard 16D nail is 3 1/4 inches long and so you're only getting 1 inch of nail into the rafters.
Also there is the issue of wind uplift forces. With purlins spaced 2 foot apart vertically and the rafters being 2 foot apart (horizontally) each two nails (holding the purlin to the rafter) must be able to in effect hold down 4 square foot of roofing. One document talked about 90 pounds of wind up lift force possible per 1 square foot of roofing. And two nails are supposed to handle 4 square foot, or 360 pounds of force. I KNOW a 16 penny nail will not hold that. So, 60 D nails are a must, unless you want your entire new roof blowing off, purlins and all when a strong wind comes along.
Here you can see on the left part of the roof where the sheathing was replaced after the fire..
We installed 2 x 4 purlins on about 24 inch centers from the eaves of the roof to the peak. There is 1 1/2 inch cut back at the peak for the ridge vent. The final purlin runs right along this so we have somewhere to attach the top of the roofing panels and also the ridge cap.
Murphy is of course working over time and several, I think 4 purlins on each side, fell right on top of the gap in the old roof boards, so we had to cut and install 3/4 plywood blocks in the gaps to keep the purlins straight. We used plywood, because if we tried to drive those 60D spikes through solid lumber it would just split.
It has been almost a month since we started jacking the roof up and we are finally putting the steel roofing on. Actually the timing also had to coincide with when our son had a break from college. Thats him working the eaves from the loader bucket.
I got to work up and down the roof doing the majority of the attaching. We used 1 1/2 color matching screws to attach the steel. One screw at each rib (5) and each purlin (10). So something like 50 screws per panel. You can't see real well, but thats a Milwaukee Decking screw gun, not a drywall screw gun. This type runs slower and has the optional nose piece that fits a nut driver bit instead of a screw driver bit, Its FANTASTIC for these screws, you set the depth so it compresses the rubber washer just right and go for it. No checking and rechecking depths, etc.
To get to this point we finished the purlins on each side. We installed a steel drip edge molding on the eaves. And we measured and snapped a chalk line up the gable that is square to the eaves. Basically you HAVE to get the steel running square to the eaves otherwise the overhang will change with each sheet.
Well, our line started out ok, but the foam inside closure strips that are installed at the eaves causes the panels to bow up in the center such that the panel is slightly narrower, by maybe 1/32 at the eave. Add that error up over 12 sheets and you get a bigger error. Needless to say our overhang is not perfect, but its waterproof !
And, No I had not trimmed the purlins to length on the other side of the roof, yet. We were fighting rain all weekend and we had a dry spell so we started putting on steel.. (I can walk on wet wood, I can NOT walk on wet steel - Can you say greased lightening..)
The steel we are installing is slate gray colored ordered from Fabral http://www.fabral.com/ via out local HomeDepot store, Sorry Menards you were NOT cheaper.
This was ordered to length, almost :-). To make sure I had the steel on time I had to measure the roof even before we stripped it. I honestly stood on a ladder at the eaves and pushed a tape measure up the roof to get a measurement, of course better too long than too short.
Well the panels I ordered were 18 foot 6 inches long and we needed 18 foot 2 so the boys got to cut 4 inches off of each panel. We rented a power sheers from the rental yard, so no snips needed, yet.
The interesting thing about picking up this order, besides hauling a 1000 pounds of 18 foot long material home, is that Fabral added cover sheets to the pile to protect it during shipment. There was one additional 18 ft piece on the bottom and 2 10 footers on the top. So we have some left over steel for another project, adding an outside stairway to the haymow.
And the same somebody asks, why not just let the roof overhang be 4 inches longer. Remember that discussion on wind uplift forces... Well that 4 extra inches of overhang maybe just what the wind needs to tear the roof off. Fabrals manuals specifically state that the overhang must be limited to 1 inch and the screws at the eaves are actually doubled. One on EACH side of the rib instead of 1 on 1 side of the rib as in the field.
We started the steel runs for both sides of the roof from the other gable end, the straight end. So when we got to this end we had to 'rip' a panel to about 1 foot wide for about 12 feet and then account for this point. To finish this off I had to add yet another small piece of steel to the point. Of course all of the finish work on this part is done while straddling the peak of the roof. A roof that is now totally covered with slick steel. I was wearing the rock climbing harness and I was roped off to BOTH sides of the building in case I slipped.
The point was especially fun because once I got the drip edge on and the roofing and the ridge cap, I went down on the ground to 'admire' my work. From that vantage point I could see the ridge cap sticking out squarely over the end of the point. and there was a real nice hole under the ridge for birds to get into. (Which is now closed up with some white aluminum coil stock from the shop.)
So how does a person get up there to work on that??? If you put the ladder on the barn wall, you're 4 feet away from the point. And I guess you could get back up on top of the roof and lean over the edge. While roped onto the slippery roof, 25 feet in the air....
I took the tractor around to this end of the barn and put the ladder in the bucket. I had to have the ladder's legs straddle the peak. If someone would have let the loader down when I was up there, I was looking at a FUN ride..
Here's the roof all finished and trimmed out. The rake, or gable trims and ridge vent are all installed. The point at the other end had to add to the fun when I installed the rake trim.
On a straight gable end (right side of the Picture) the trim starts at the eave and run up the roof and terminates under the ridge vent. If you follow the trim thats is on the extreme right edge of the picture you'll see it go up under the ridge cap.
But what do you do with the other end of the building where it angles out??? and, no there are no instructions in the manuals to help figure this one out. The big issue is how do you terminate the end of that trim so rain can not get underneath it??
Well, if you follow the trim on the left side of the picture up the roof you will see that it just continues up the roof and under the ridge cap. Well, thats AFTER some modifications. Basically we had to trim off the part that would have hung down on the face of the building. We re-formed the trim it to come down on the roof panel similar to the way the roofing panels over lap. In our case we got lucky and the re-formed trim came down right on top of a rib in the roofing panel and screwed it into place.. The main thing is that its waterproof..
If you zoom in on the previous picture it might help show how that trim was finished. You are aware that if you click on the pictures you can blow them up back to original size, right??