Useful Links
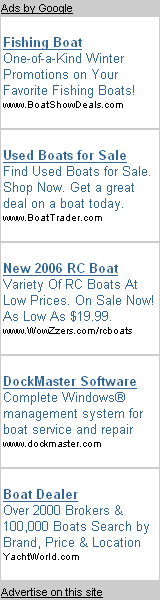
In too deep to quit.
1st thing to go was the rotten transom. A circular saw, hammer, and flatbar was all it took
The flotation blocks were soaked, the glassed plywood enclosures were rotten, and the main deck was UNDER them. They had to come out. Little did I know, hours of grinding are ahead.
This is the original factory deck that was under the added upper deck. Under it, is poured flotation foam.
The added-on bow deck is gone, the small step up factory deck and underlying foam is gone. What's left is the rotten nose piece of the main deck.
Pre-planning is the most sensible way to work the glass and resin. Sticky latex gloves and scissors don't mix well. Sticky gloves and rolls of glass don't mix well either. At this point, I had pre-fitted all of the wood parts, and was satisfied with the fit. A lot of time and effort went into that. Some of the small pieces at the rear were so rotten, I could hardly tell the dimensions and how they fit back together. Note the 1" portable strap holding the sides. Prep work is the ABSOLUTE KEY. Why invest all of the time and money to do a lousy prep job? Polyester resin is easy enough to work with, but it requires a CLEAN, SCUFFED, surface to bond to for the initial bond. The 1st bond is purely mechanical. Since the skeletal replacement is not a true laminination process, CLEAN, and SCUFFED is the only suitable choice. I used a 34 grit flapper wheel on my mini-grinder, and ground 4" back from all old bonds. Both sides of the stringers were ground, as well as both sides of the transom.Wipe all surfaces to be glassed with acetone.
I kind of went overboard here. The sheet of glass is one piece, from left to right. The idea was to tie everything together, as a monlithic, (yeah, I did structural concrete for awhile). In hindsight, I could have done it a number of different ways. Oh well. Maybe next time.
The cross braces are notched into the stringers, and glassed to the hull. They sit flush with the top of the stringers and just touch the inside of the hull. The first one lays on top of those 1/2" plywood stiffening blocks. It takes time to fool with them. All of the woodwork was pre-cut and dry fit before any sticky stuff entered the picture.
After a lot of reading and consideration, I chose 3/4" exterior grade 5 ply B-C sanded for the transom. I learned something as I was taking this boat apart. Whoever added on the front deck , did an excellent job. It was glassed on the underside as well. As I was ripping it out, I noted that they had seriously scuffed the surface of the plywood prior to laying up the glass. It only makes sense. So, after tracing the pattern from the old transom, I scuffed it royal. With a 34 grit flapper wheel. Wiped both sides with acetone, and laminated the 2 pieces together with chopped mat. Clamped it, let it set, and that is what you see.
I gotta be honest here. This did not go as well as I would have liked. The bottom of this hull is curved where it meets the transom, and with the inverse angle of the transom, the glass did not want to conform to the curves. Chopped mat does not like outside transitions. It will do OK on an inside corner, or radius, but trying to get it to lay smooth over an outside corner did not go well. The more I tried to get it to lay, the worse it got. The adhesive that holds mat together is designed to dissolve in poly resin. I ended up with gooey hairballs. I was trying to lay up whole sheets, from side to side, completely covering the transom and tying it to the existing hull. I wanted to lay cloth, then mat, then cloth again, mat again, more cloth. I wanted a 3 layer cloth lamination, and hadn't caught on to using styrene as a thinner to roll the resin and glass. Another newbie mistake was to take the roller right out of an acetone bath and try to roll resin with it. The batch was just starting to kick and I got in a hurry.It wrecked the 3rd layer. Chuck the roller, and put on a new sleeve. The 3rd layer had to be ground back off later.
By now, it's upside down, in preparation for gelcoat repair and paint work. But I had to fix that mess from the previous botched layup. I dutifully ground all of the boogered up, bubbled, lumpy glass off. I then went back and reground the sides where the transom ties to the old hull. Back to "virgin" glass. 2 strips of 4" wide 18 oz went on 1st, vertically, at the seams where it ties to the hull. Then a pre-cut 18 oz piece went across the whole transom. Then 2 8" pieces of 18 oz strips, covering the edges of the whole transom piece,lapping the previous 4" piece, then another whole piece across the entire transom, again pre-cut to fit, then two 12" pieces, again, lapping the second whole transom piece and the previous 8" piece. I cut the mekp ratio, down to 1.25% for a longer pot life, and thinned the resin with 10% styrene. I thinned and mixed very well before mekp was added. This went real well, it might as well been shot on with a chopper gun. But the 18 oz cloth is stronger than the shredded stuff that comes out of a gun. I'll work that goofy curved part, fix the hull nicks and gouges, gelcoat what's needed, prep it for primer, prep it for paint, then paint it with Pettit Easypoxy 1 part polyurethane.
This keel was pretty beat up. I ground out the smashed crushed glass, and laid a hefty bed of thick milled glass putty. Then a layer of 18oz roving, then a layer of 6oz cloth for a smoother finish. There is a lot of fairing work ahead.
After grinding the bolts off, the area was ground and repaired with mat and cloth. All fairing work is done with hand mixed, homemade cabosill-gelcoat filler with wax sanding agent added. I call the stuff cabogel. Mix it as I need it. To whatever ratio of cabosill and hardener I think I want.
Some knucklehead had run a screw through the bottom of the hull. I drilled it out, cleaned up the hole and repaired it with a homemade milled glass putty. It looks a lot like something that would come out of a choppergun. The stuff works great
I got a little too aggresive with the minigrinder. It just adds to the work. I went overboard, (as usual) and repaired this from this inside, and out. I've read that an inside repair is all that's needed. Oh, well. I cut the hull four times while cutting out the deck. It was so curvy, I couldn't tell where the grinder blade was. This kind of crap is to be avoided
Not too many straight flat surfaces to work with on this boat. A lot of hand sanding with a small block. The small orbital sander helped some, but with all of the curved surfaces, it was kind of limited.
I've learned my lesson about taping off areas I don't want gobbed up with errant resin.
A lot of work went into this part. The cabogel stuff I make up is what was used to smooth the transom out. That, and lots of sanding. The last coat was thinner on the cabosill, and I rolled it on, then tipped it out with a badger brush dipped in styrene. It helped with the sanding. Much smoother.
I had a couple of cold ones after this pic. I've gotten pretty good at guessing how many sheets of spent sandpaper to pad the fresh one with. It keeps the fingers and hand from getting hot. It also helps round out the little 2X2 sanding block some, for all the curved surfaces.