Useful Links
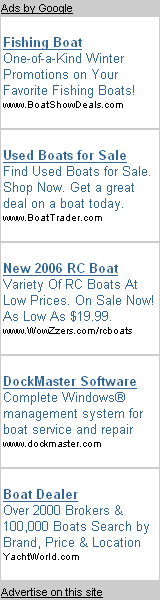
Newtonian Astrograph
My former astrophotography rig consisted of a Meade SN8 imaging with a modified Canon 350D. The guidescope (dubbed the 'SS Crapper') was my first feable attempt at ATMing. The SN8 was a great instrument for learning and provided me with many successful imaging sessions over the year that I owned it. This model is very heavy for its aperture though and collimation is a chore due to the poorly designed secondary holder. By all accounts I am still a beginner, but eventually these issues and more became the limiting factors rather than my own skills. I've outgrown the limitations of this equipment and the 8" F/5 astrograph I'm building will represent an upgrade in every single category.
NEWT 2.5 is a free ray-tracing application that allows the user to layout a classic newtonian telescope. Thanks to some guidance from others more experienced than myself I was able to use NEWT to ensure that the 100% illuminated area being cast by the optics would fully cover my CCD chip. This is arguably the most critical attribute of a true astrograph. In my case I needed a 100% illuminated area of at least 28.11mm (1.11 inches) in diameter. In this case I needed a 2.6" minor axis for the secondary mirror in order to project a 100% illuminated area of 1.3", just lslightly larger than needed.
I decided to design my own mirror cell rather than purchase a prebuilt model. There are several makes and models to choose from but I've not found any mid-range mirror cells that I liked. Most are either not substantial enough for imaging or are too expensive. Besides, making my own is more fun.
I will say up front that there is very little in the way of science or proven methodology in this design. I simply tried to use my own sense of weight and rigidity such that the latter would not be compromised. Six spaces were removed in the upper plate to save on weight leaving six spokes that measure 0.5" thick. In theory the spokes will still be plenty rigid while allowing some throughput for air circulation to the base of the primary.
TurboCAD 14 was used to draw each half of the mirror cell. This design assumes 6061 aluminum for the material at a thickness of 0.25". Royce's conical mirrors offer a particular appeal for use in imaging telescopes in that they are cast with a mounting bolt protruding from the base's center. This bolt is intended to be passed through a compatible mirror cell and then locked in place using a washer and nut. Royce's design illiminates the need to epoxy the primary in place. The 8" F/5 mirror uses a standard 3/8-16 bolt so I have placed a mounting hole in the upper plate accordingly.
After a great deal of research and waffling over pointless details I decided on 1/4-28 collimation bolts. This will allow for seven threads to be engaged in the 0.25" cross-section rather than just five threads with say, 1/4-20 for example.
The center hole in the lower plate measures a somewhat arbitrary 3.125" in diameter. This is to allow easy access to the mounting hole for tightening down the locknut as well as allowing air flow to the base of the primary. At some point I may mount an 80mm fan over this hole to aid in faster equalization before beginning an imaging session.
My plans call for a 10"x43" telescope tube. For the time being I have chosen to use aluminum irrigation piping available from a compnay in Nebraska. Hastings Pipe Company has developed a great reputation among the ATM community for the service they are providing to us. This tube was ordered with each end rolled to increase strength. The wall thickness is 0.064". Here it is pictured next to my disassembled Atlas EQ-G for scale.
A long-term goal for this astrograph to have a custom carbon fiber tube. This material provides superior strength and substantail weight savings compared with aluminum. The kicker though is a much lower coefficient of thermal expansion. Focus shift over prolonged imaging sessions is far less of an issue with carbon fiber telescope tubing.
I purchased two sections of 12"x12"x0.25" 6061 aluminum flatbar from a local metals supplier. Cosmetically speaking this stuff isn't the best, but true aluminum plating is much more expensive. Each 12" section cost me about $22.
I took my plates to a local metal fabrication shop to be cut on a water-jet machine. The technician loaded my CAD drawing and away it went. This machine cuts with a 60,000 PSI beam of water about 0.030" thick.
Hammerhead Water-Jet machine: $350,000
Getting your own custom-designed aluminum shapes cut to 0.030" precision - priceless.
To my dismay the technician was able to cram both halves of the mirror cell onto one 12"x12" section. Now I have a backup plate in case I find that I've royally botched something.
The hardware just arrived. For lack of experience building mirror cells I ordered two different sets of compression springs to feel them out. One set is substantially stiffer than the other, but both are fully capable of lifting the combined weight of the upper plate plus mirror at as little as 0.25" of deflection.
Pictured from left to right (top row first):
1/4-28 stainless knurled thumbscrews, 1.75" shank (collimation bolts)
Stainless compression springs, 1.5" long, 0.375" OD, 17.68 lb/inch
Stainless compression springs, 1.25" long, 0.6" OD, 37.49 lb/inch
1/4-20 stainless knurled thumbscrews, 1.5" shank, (locking bolts)
8-32 stainless socket-head machine screws, 0.75" shank, (mounting bolts)
Close-up of collimation thumbscrew, locking thumbscrew, and one of the stiffer springs (37.49 lb/inch).
UP NEXT - Choosing and purchasing the secondary mirror and spider vane. It is also about time to place an order for my Royce conical 8" F/5 primary :-D. The figuring and coating processes take place at different locations so it will be at least a couple of weeks before I can take delivery of the mirror. I'll probalby place the order soon so that the mirror will be available a few days before I'm ready for it (rather than having to wait).